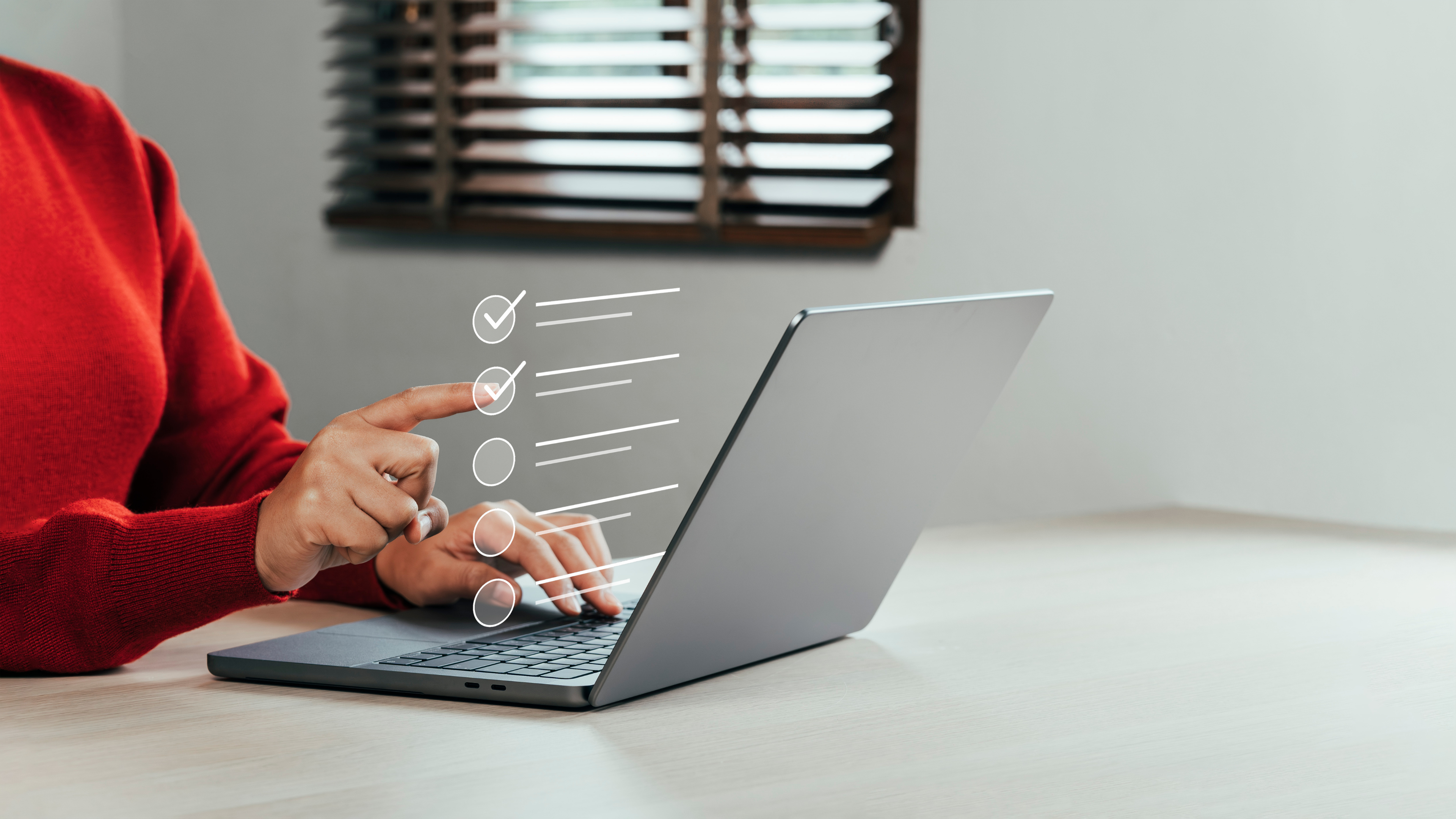
5 Reasons to Revamp Your Quality Assurance Document Control Procedures
Manufacturers need to maintain accurate and transparent records throughout the entire product lifecycle, with proper documentation and quality assurance (QA) document control procedures. All too often, however, those files are created across multiple people, systems, and locations, which can lead to disorganized data.
The manufacturing industry is transitioning to digital solutions to more effectively manage rapidly evolving manufacturing processes and supply chain management. Here are five reasons to revamp your document control procedures to improve the QA process.
1. Take Control of All Data Types
The digitization of QA documents brings all records — paper and digital — into a central location where team members can access what they need from anywhere, at any time. Work instructions, quality records, product plans, compliance forms, and more will no longer live in files on various drives or in actual filing cabinets.
Quality assurance document control solutions should be flexible and adapt to business needs instead of requiring that processes be built around the system. With the right machine learning (ML) partner, businesses maintain the ability to react faster to—and even get ahead of—changing market conditions.
2. Create Dynamic Views of Document Data
Manufacturers that use digital quality assurance services gain insights into quality control (QC) and QA processes. ML classifies documents, extracts data, and establishes document relationships across disparate sources. Company leaders can use this information to discover and take advantage of opportunities that could very well have gone unnoticed before the digitization of business records.
3. Optimize Downstream Systems
One component of quality assurance document control is that complete and accurate data fuels other systems, including the following:
- Robotic process automation: Improves efficiency at the machine, process, and factory levels
- Content systems: Creates visibility and an audit trail for better access management and compliance
- Customer service: Enables real-time proof of delivery documentation and faster issue notification and resolution
- Business intelligence: Provides reliable track and trace data for analytics and reporting
ML isn’t only limited to how it can improve operations on the manufacturing floor. It can drastically reduce the amount of time office staff spends on some administrative tasks such as reporting and record keeping, as well.
4. Generate Instant Access to Complete Document Data
No matter where a business has operations, personnel stationed in different geographic locations and various time zones all have access to the same information. Utilizing universal document retrieval, individual changes are tracked, creating a complete audit history. This history can eliminate doubt and confusion, while at the same time decreasing the potential of lost production time.
5. Improve Efficiency and Accuracy
One of the most significant benefits of quality assurance document control is the standardization of QA documentation. Meeting regulatory and compliance regulations has always been one of the stiffest challenges for manufacturers, but with an AI-driven solution, following the chain of custody is no longer a painstaking manual process. Quality assurance digitalization reduces the time needed to fulfill audit requests with instant access to the same information quickly and easily.
Implementing quality assurance digitalization optimizes the approval process by giving company leadership the ability to check documents and sign off on them from anywhere. This way, production remains on budget and on time.
Find out how Ripcord’s document ingestion and document intelligence technology helped a global medical equipment manufacturer rapidly pivot its device certification processes to meet new EU compliance requirements.