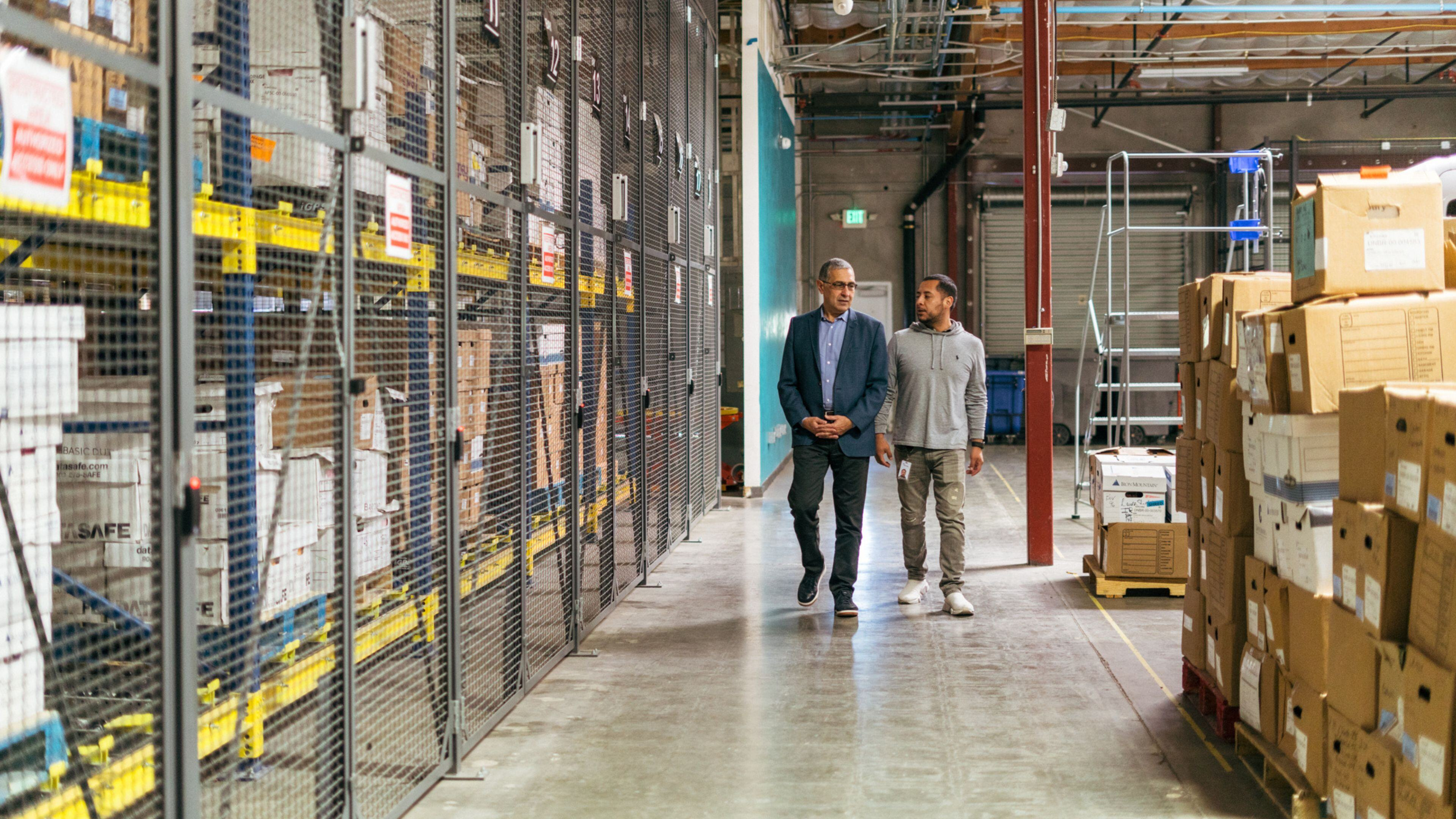
Secure Success: Physical Security for Documents & Data at Ripcord
Welcome to the first in our series of articles that examines the extra layers of security that we provide for each document handled on-site at the Ripcord facility.
When breaking down security maintenance for a business, often the question of how to protect private documents will be the first thing to come to mind. And rightfully so — the information inside those documents is typically as valuable as anything else the business possesses.
Whether that information is stored in paper or digital format it remains susceptible to numerous types of security breaches, and can result in considerable damage to the reputation of the business at hand, if accessed by the wrong people or destroyed by natural causes.
That’s why the proper handling of client documents at Ripcord remains a top priority. Tons of documents are shipped to the facility for robotic digitization, and critical steps must be taken at every stage of the process to ensure no information is lost or worse: stolen.
Security at Every Step
Executive VP of Global Operations at Ripcord, Jens Hurley, speaks highly of the physical security protocols that are in place at our organization, and details how every box of documents that arrives is given a unique identifier, to track it throughout the entire digitization process.
“Upon reception of the actual content to the production floor, to our facility… Every shipment is depalletized or itemized, and we record every single package that hits our production floor," said Hurley. "From here we create a manifest and ship that back to the customer to get their approval that everything that was sent was received.”
From the arrival through to the end of the shredding process at Ripcord, human interaction with the documents remains very limited. Hurley shared that once the documents are identified they’re placed directly into a secured, access-controlled, climate-controlled, inventory location and video surveillance captures every movement they make from there.
“We want to guarantee the safety of the content that’s inside, and limit the amount of physical activity that somebody might have with it. We do that by not only eliminating the amount of product that we put on the actual production floor, but we also track and monitor that box, in terms of what process it’s at on the production floor, what machine it’s at, who touched it, when they touched it, what processes were performed on it.”
“…We highly scrutinize and limit the amount of people that actually have access to our production floor, and we even limit access to the people that have direct contact with that particular customer content.”
Once the documents reach the robots, the risk of a security breach remains extremely low, thanks to the automation of the process. As Hurley explains, if the documents were being fed to a typical scanning machine, a person would be handling them one page at a time and removing hardware such as staples, and this provides much higher opportunity for danger. Because the robotic digitization process is automated, the amount of touch time required is largely reduced, and it adds extra security to the documents.
Following the robotic scanning, additional steps are taken to determine whether the documents are ready for shredding, and that what has been shredded is actually what was asked to be destroyed by the client in question.
“Our company motto here is to take the world paperless, so with that we want to basically digitize and shred and recycle as much paper as we possibly can.”
“There are many cautionary steps along the way to verify exactly what we have digitized is ready for shred," Hurley shared. "We also go through many quality checks to guarantee that every document within that content that’s going to be shredded has been digitized, digitized accurately, and digitized well. All in that time we’re in direct contact with the end customer, and upon the completion of the shredding event we provide the customer with a destruction document that verifies the contents that were destroyed.”
Business Continuity
Another important thing to consider with all documents, of both paper and digital nature, is their protection against the elements. At Ripcord, all content is stored in locked and secured areas above ground level, to avoid potential flooding and earthquakes, and the buildings have standard fire-suppression systems to guarantee minimal loss.
Hurley says business continuity is taken very seriously at Ripcord, for both external and internal documentation, and that there are several things to consider when developing such a plan.
“Once we actually identify what those core requirements are, or the business sectors are, we really dig down into those and develop strategies on how we can plan to mitigate risk for those particular sectors. Here at Ripcord, just as a simple example, we do that both for physical documents as well as digital documents. Some of those plans are directly implemented on the production floor, as quickly as we possibly can, and some of those actions are put into a timeline to say, ‘This is exactly how we react to a situation,’ so we can react accordingly and more quickly.”
For digital content, a backup plan has been implemented to reduce risk. Ripcord maintains backup power supplies to ensure no content is lost if power was to go out.
“We make sure those core process and applications can continue to run and continue to cycle to guarantee the customer has access to their data and that we’re still adding value to them.”
Physical security is clearly something that matters greatly to Ripcord. Companies working with us to digitize their numerous boxes of documents can rest assured, because great precaution is taken to avoid any potential harm during the on-site process.
Ready for more? Head over to the Ripcord YouTube channel to hear the full interview with Jens Hurley!